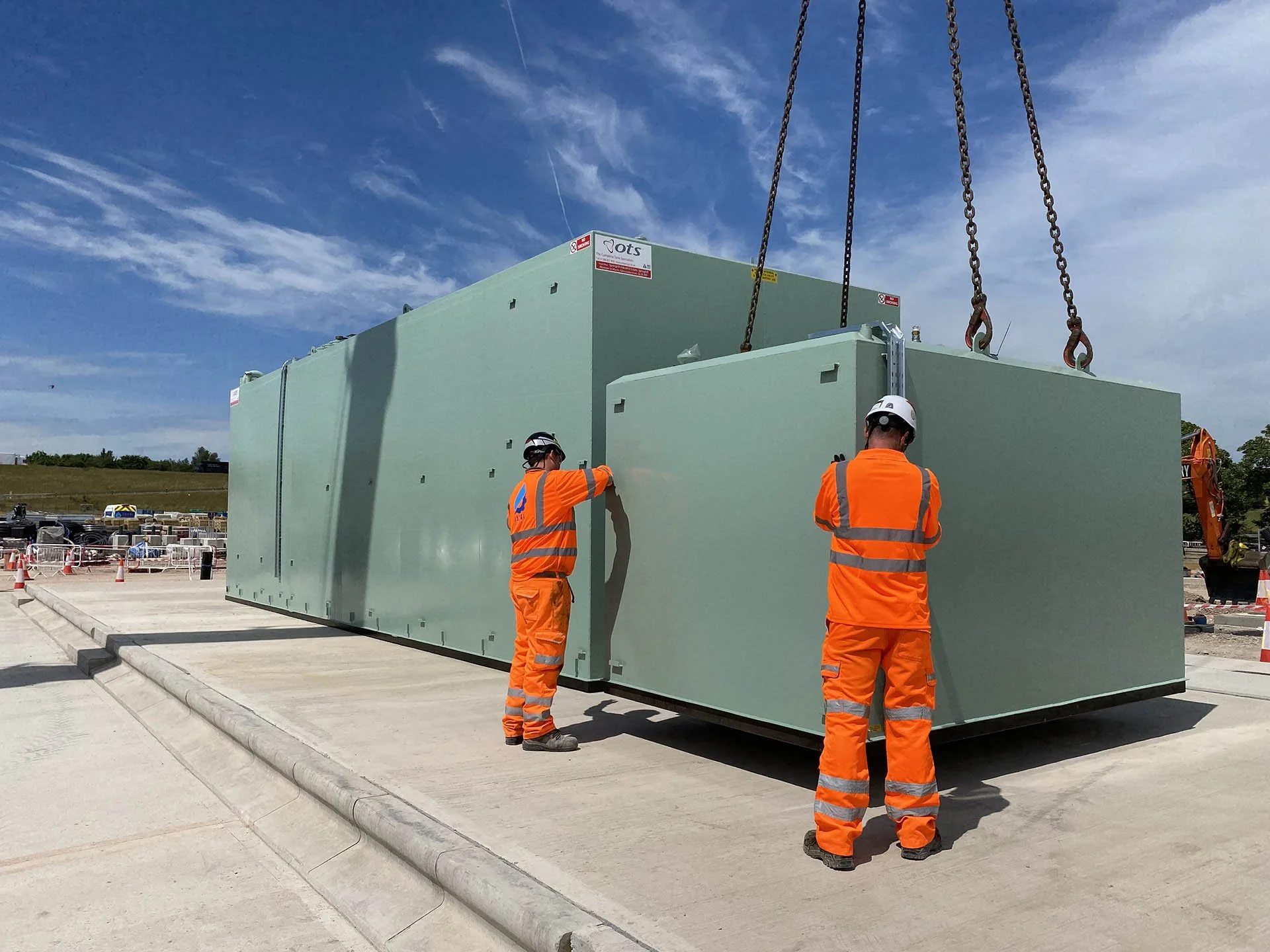
HS2 Bulk Fuel Storage and Dispensing System
The HS2 Bulk Fuel Bunkering Site is an essential component of the HS2 project, providing fuel storage and dispensing facilities for construction equipment at key HS2 sites.
The site is set up to store two products, Diesel (DERV), and AdBlue, in separate Above-ground Bulk Storage tanks (ASTs).
-
The HS2 Bulk Fuel Bunkering Site is designed to store and dispense diesel to support the needs of the HS2 rail project and features state-of-the-art storage tanks, pumps, and dispensing equipment, which are designed to provide reliable and efficient fuelling services to the HS2 project.
This case study will provide an overview of the HS2 Bulk Fuel Storage and Dispensing System, including its key features and specifications.
The fuel storage tanks for the site will be capable of holding 125,000 litres of DERV and 10,000 litres of AdBlue. These tanks are essential for ensuring that the site has a reliable and continuous supply of fuel. All OTS tanks are designed and built to accord with the Control of Pollution Regulations which require a Design Life Expectancy of 20 years, and OFTEC OFS T200. Proper maintenance and monitoring of the tanks will be conducted regularly to ensure their continued safe and efficient operation.
-
OTS Group implemented a bespoke fuel dispensing solution for HS2 to enable them to meet their ambitious construction schedule while ensuring compliance with all safety and environmental regulations.
Designing and building a custom bulk fuel storage and dispensing system that could meet HS2's strict safety and environmental standards.
Integrating a tried and tested Fuel Management System that was supplied and installed by Centaur Fuel Management Limited.
Providing ongoing maintenance and support for the system to ensure optimal performance. The latest iteration of Poseidon SCS™ remote monitoring has been installed to provide remote oversight and control of the system to minimise any downtime.
-
The installation process for the tanks, equipment, and materials required meticulous planning and execution to ensure that everything was delivered safely and efficiently to the site. OTS Group transported all the required equipment on a total of five vehicles, which were sent at intervals to allow for the unloading process. A mobile crane was set up on site to unload all the tanks, equipment, and materials, and once this was completed, the installation could begin.
The pipe fitters were responsible for installing all the pipework support systems, which ensure a secure and safe installation of the system. The Mapress pipework system was then installed, which involved installing pipes of varying sizes ranging from 104mm down to 42mm. The pipework connects the off-loading cabinet to the tanks and the tank to the dispensing equipment. All the control valves and safety valves were fitted to the pipework to ensure the safe operation of the system. The Mapress pipework is made from stainless steel, and the fittings were crimped into position to ensure a perfect seal on every joint. Once the installation is complete, it is subject to a 25-year manufacturer's warranty.
As the pipework installation progressed, the electricians began the electrical installation process. The initial step was the installation of the cable containment system, which consisted of cable tray supported on Unistrut and proprietary supports. This facilitated the positioning of cables, which were then pulled through ducts constructed during the building phase and securely laid and fastened to the containment. Subsequently, all the installed cables were connected to the various system components, including the distribution board, control panel, dispensers, control valves, and safety devices.
-
The HS2 fuel bunkering sites need to comply with various regulations related to environmental protection, safety, and security. These regulations are complex and constantly evolving.
-
The HS2 fuel bunkering sites require significant infrastructure investments, including storage tanks, pipelines, pumps, and dispensing systems.
-
The storage and handling of fuels can be hazardous, and there is a risk of fire or explosion if proper safety protocols are not followed. The HS2 fuel bunkering sites need to ensure that their operations are safe for workers and the surrounding environment.
-
The HS2 fuel bunkering sites need to ensure a reliable supply of fuel to meet the demands of the construction project.
-
Fuel bunkering sites can have a significant environmental impact, including land and water pollution. The HS2 fuel bunkering sites need to minimise their environmental impact and comply with regulations related to environmental protection.
HS2 fuel bunkering site challenges
-
Fuel dispensing and control are critical aspects of any fuel handling system. The dispensing of Derv and AdBlue requires a level of precision and accuracy to ensure that fuel is dispensed safely and efficiently. This section reviews the fuel dispensing and control measures for Derv and AdBlue, as well as equipment power control, tank gauge information, and remote access which is provided by Poseidon SCS™ a collaborative system from OTS Group and Certas Energy.
-
The dispensing of DERV will be done via two suction dispensers, which are one side of two twin dispensers, as well as bulk dispensing from two Bowser Filling Skids. The dispensing of AdBlue will be done via the second side of the two twin dispensers and two separate mono dispensers.
-
The fuel dispensing system comprises three main components - Derv Dispensing via Dispensers, AdBlue Dispensing, and DERV Dispensing via Bowser Filling Skids. Each of these components is controlled by a Sapphire Fuel Management System (FMS), supplied, installed and commissioned by Centaur Fuel Management Limited, which authorises transactions and prevents unauthorised dispensing. Once a transaction is authorised, a demand signal is sent to the corresponding solenoid valve on the tank and the relevant pump motor is started. In the event of an associated alarm from the tank gauge or float switch, the solenoid and pump motor are prevented from operating. An emergency stop circuit is also incorporated into the design to provide a manual way to prevent the energisation of the solenoid and pump motor. The dispensing process is highly automated and designed to ensure that only authorised personnel can dispense fuel or AdBlue.
-
Equipment and power control is provided by Poseidon SCS™ and is a centralised means of regulating the power supply to the dispensers and card readers. By using a contactor panel, the power circuits can be safely and efficiently controlled to ensure that all equipment is functioning as intended. The control panel interface allows for the selective deactivation of specific equipment through designated buttons on the touch screen pages. This provides a convenient and efficient means of managing the equipment, allowing for quick and easy control as needed. The automatic switching of the indicator lamps to red when power to the equipment is turned off ensures that users are aware of any potential issues and can take appropriate action. The equipment power control is essential for the safe and efficient operation of the dispensers and card readers, ensuring that they are functioning optimally and providing site users with a reliable and convenient fuel dispensing solution.
-
The tank gauge is connected to the control panel in order to extract & display information about the two tank compartments. The information obtained includes Tank level (litres), Ullage (litres), and Temperature (°C).
-
Remote access to the control panel is essential in order to monitor and control the fuel dispensing and control system. To enable this, the system is fitted with a Draytek router with a USB 4G dongle.
In addition to the provision of remote access, it is also important to have proper security measures in place to prevent unauthorised access. The system will have an encrypted login process to ensure only authorised personnel can access the control panel remotely.
Furthermore, the remote access functionality will be restricted to only certain personnel with the appropriate security clearance. This will be achieved by assigning different security levels to users based on their role in the organisation. The operator security level will only allow for basic monitoring and control for example, while the engineering security level will allow for more advanced features.
Spotlight on fuel dispensing & control
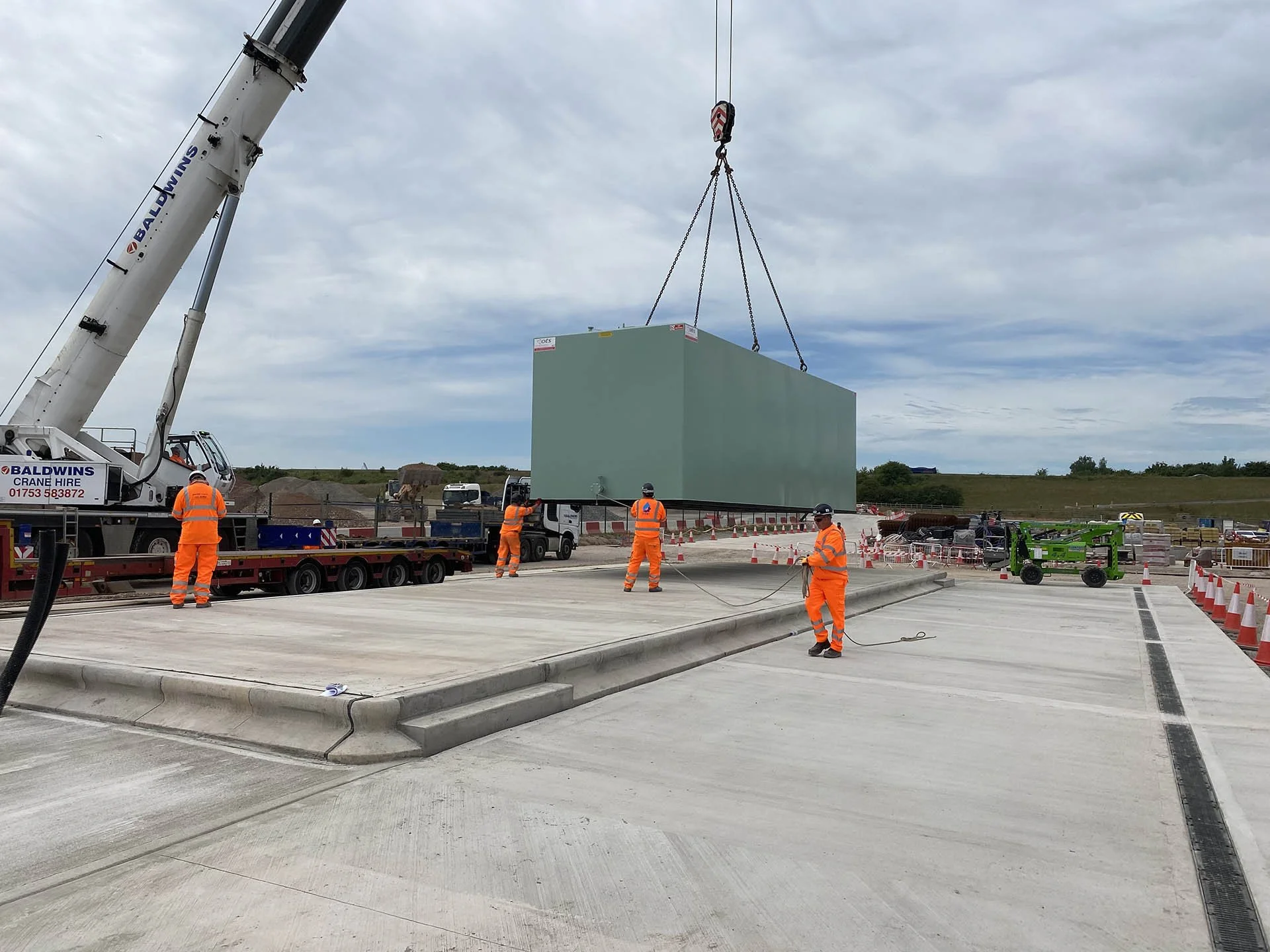
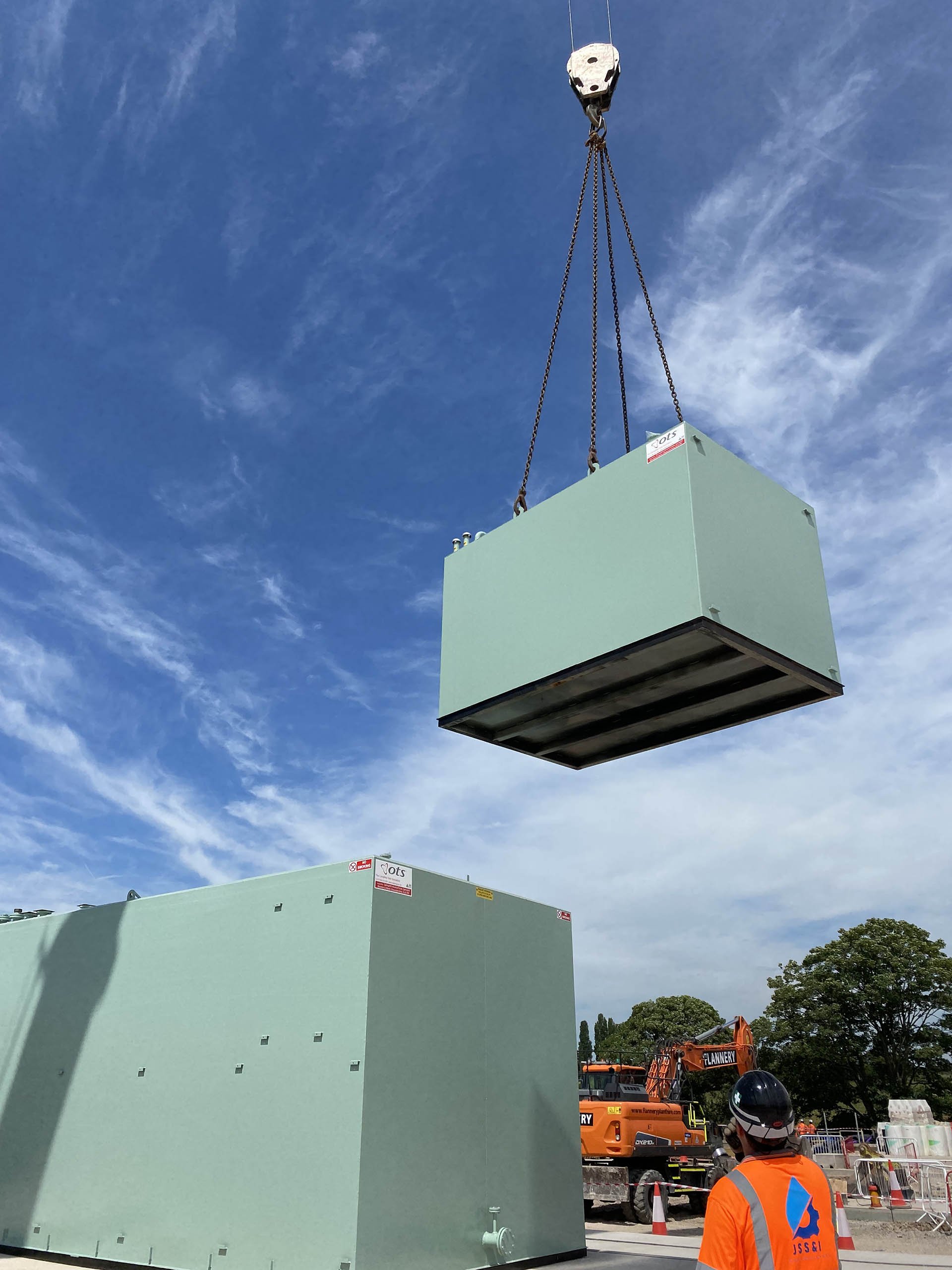
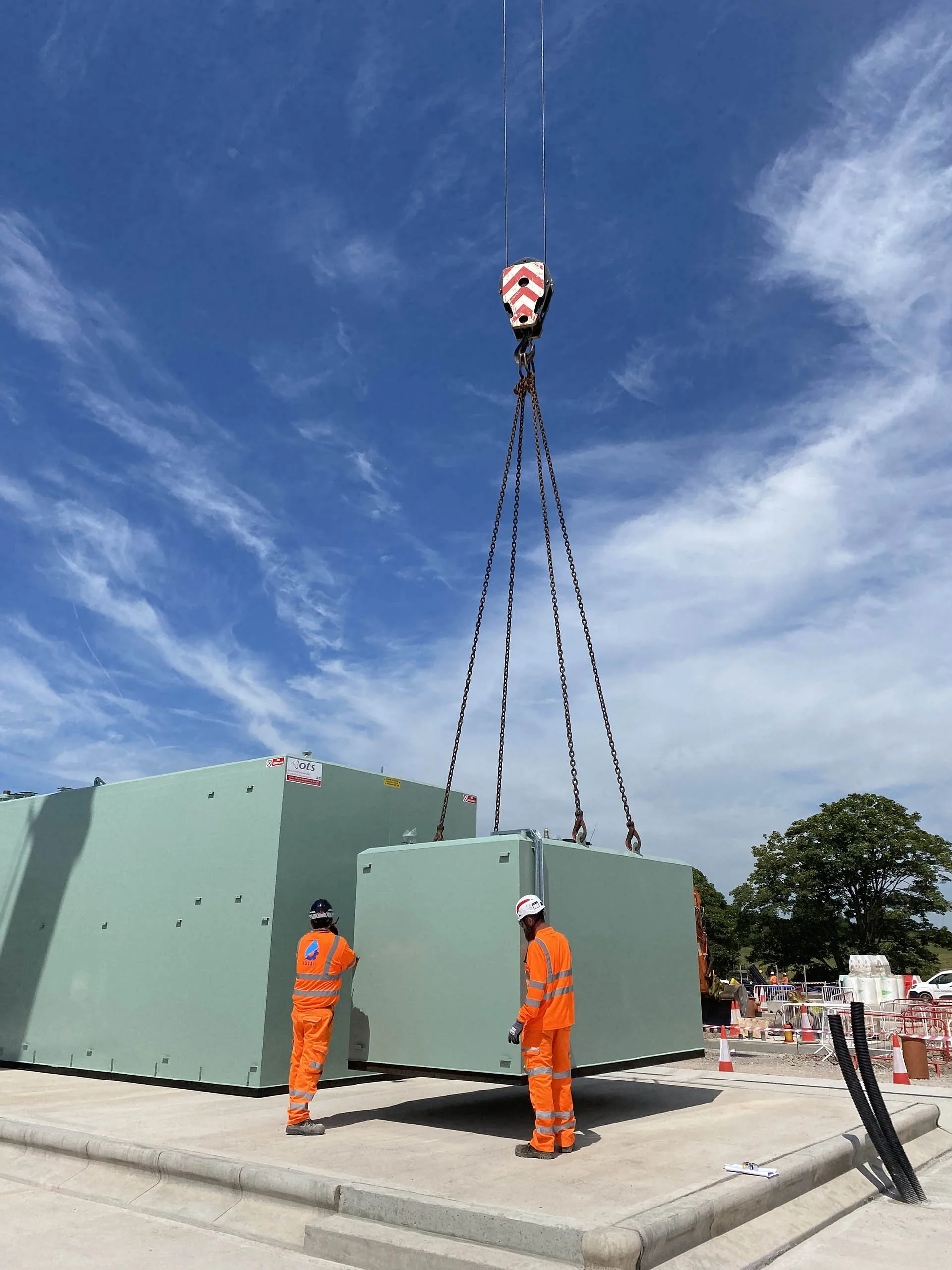
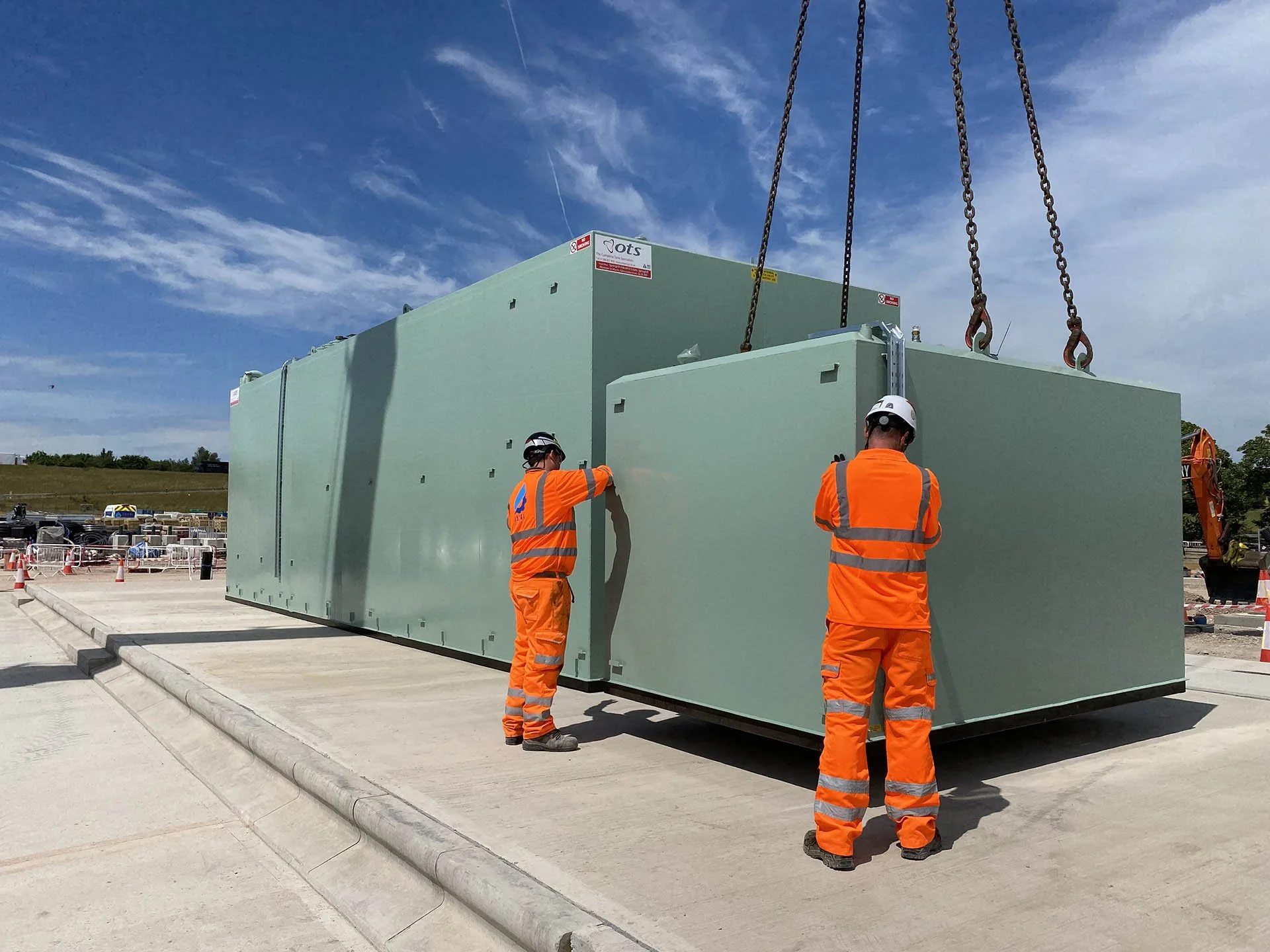
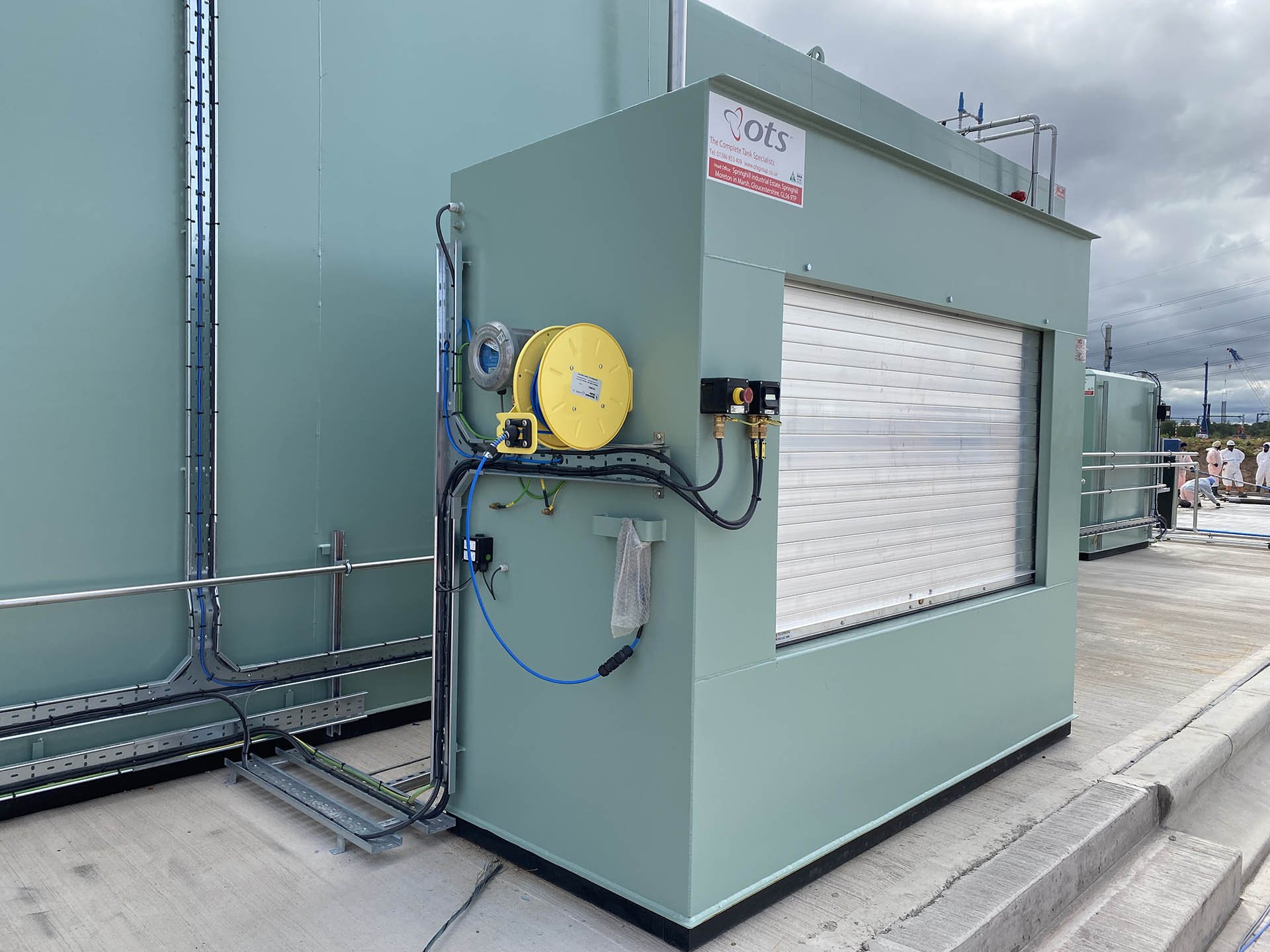
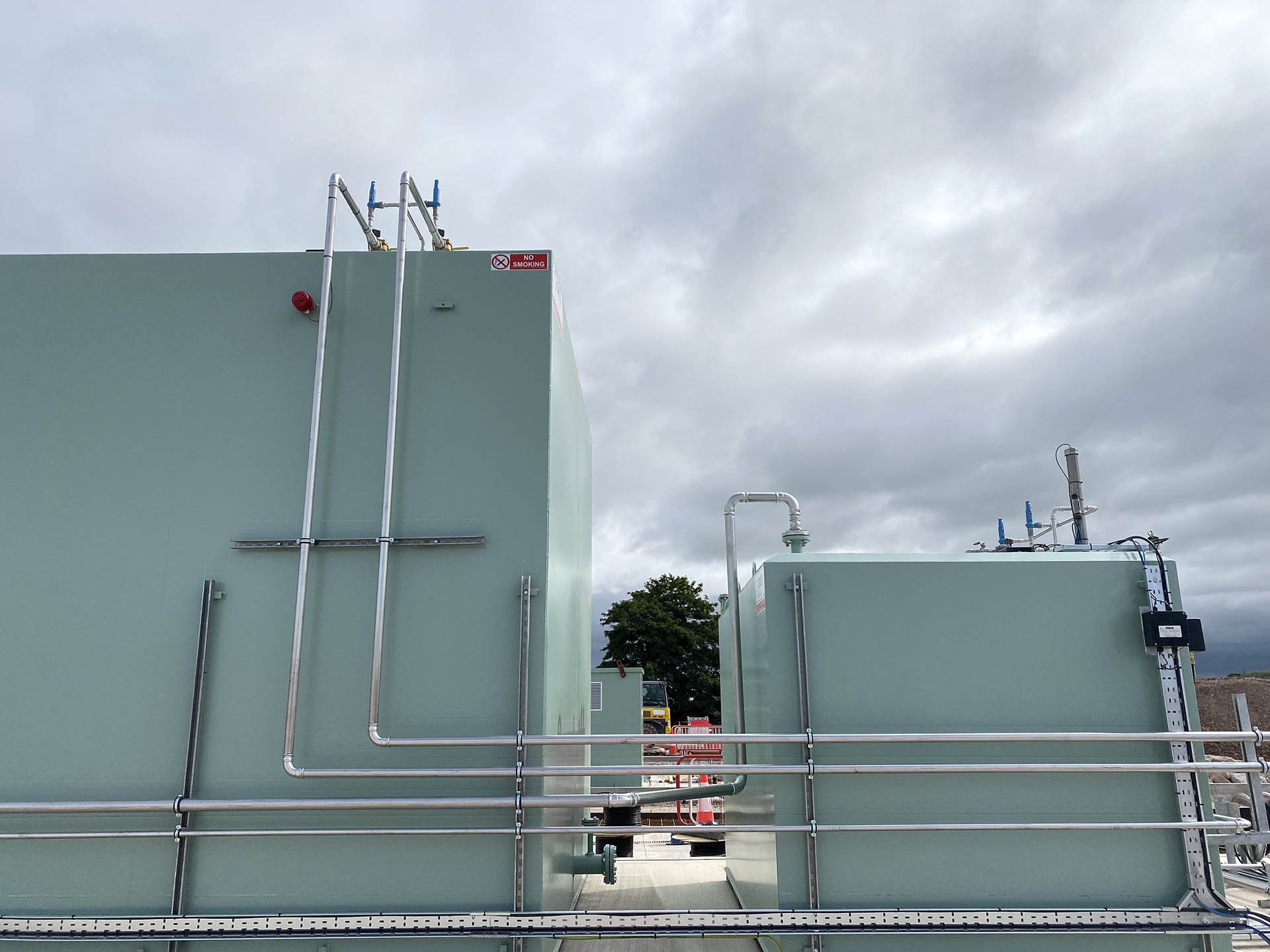

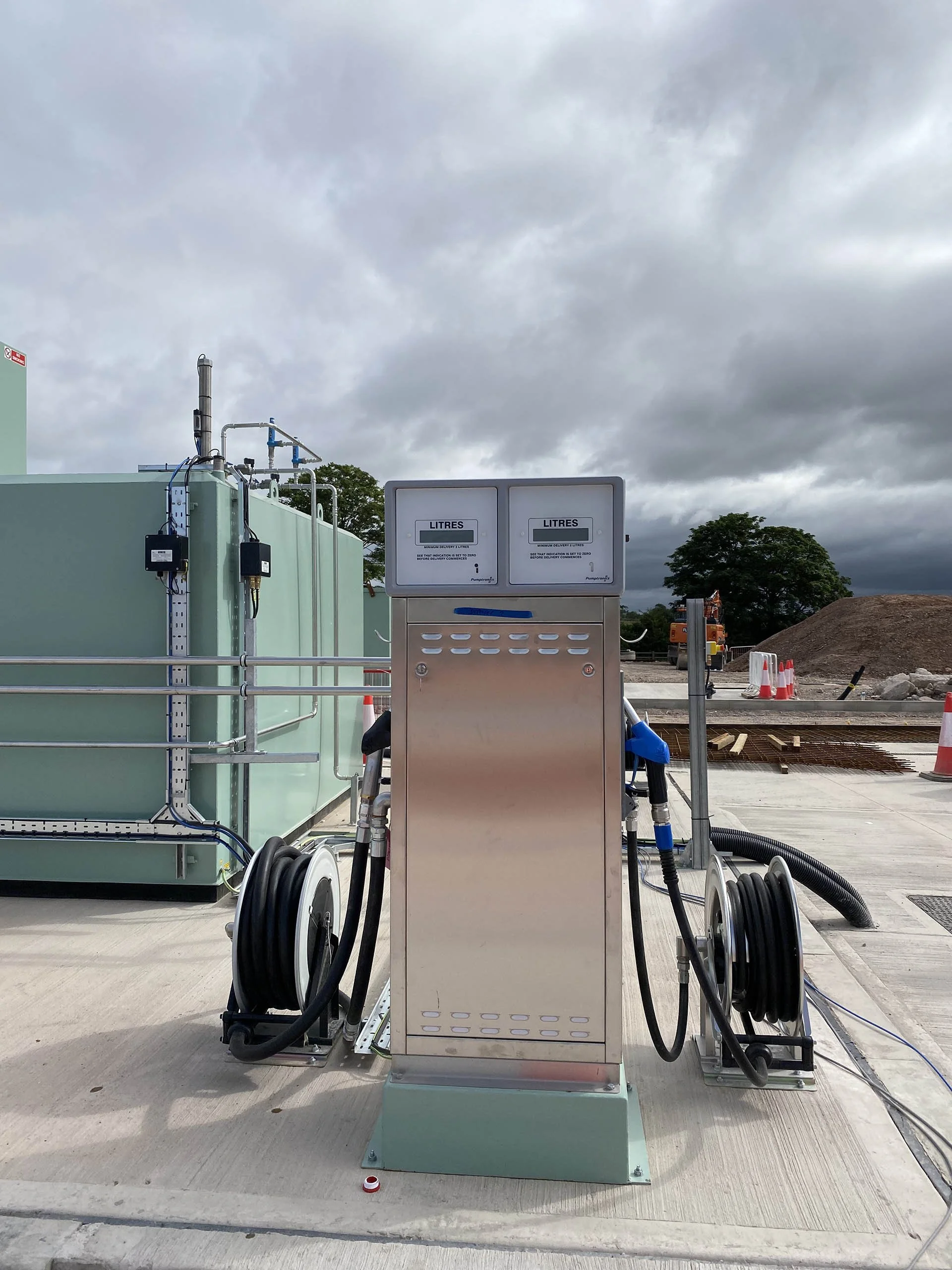
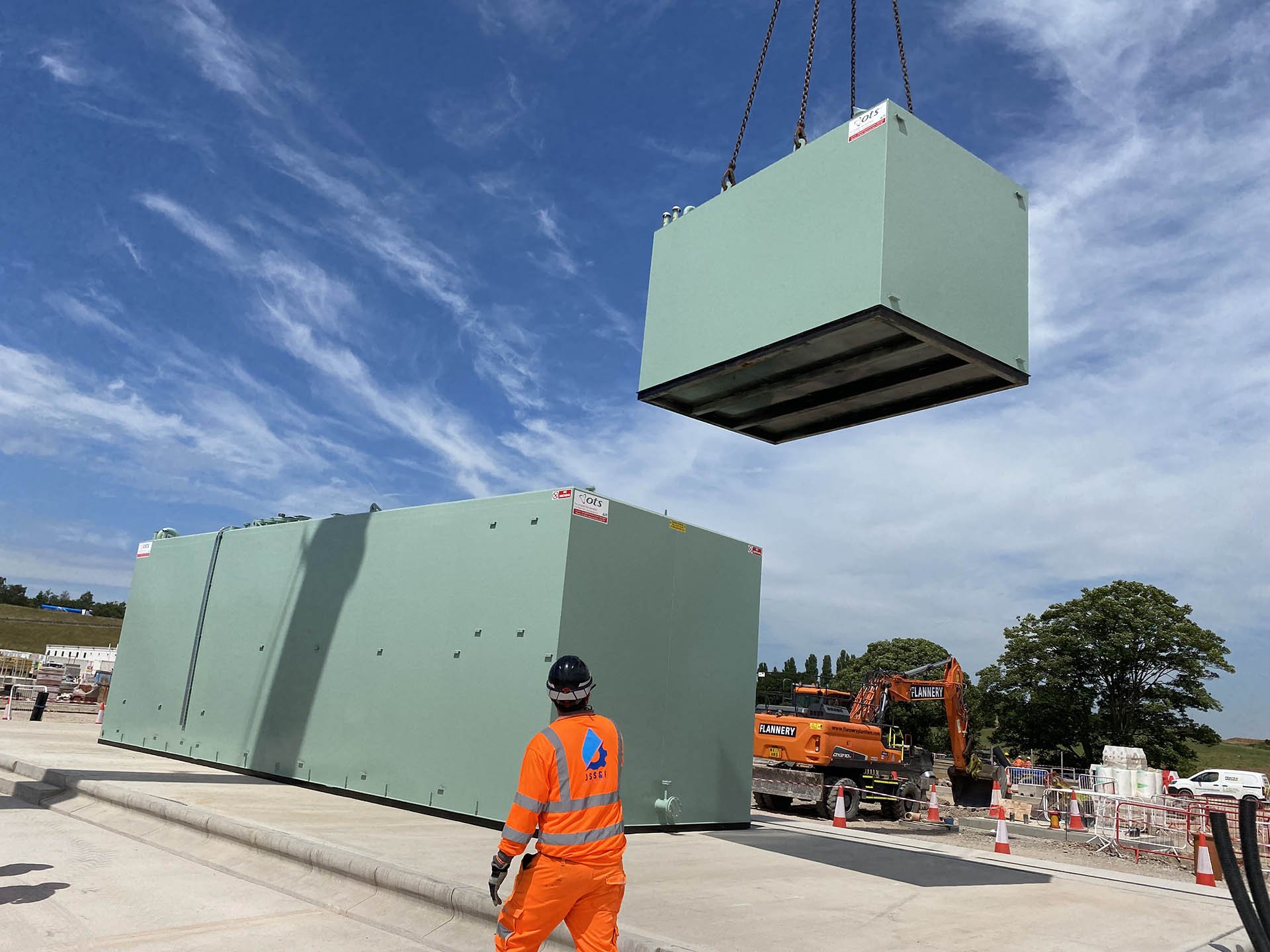
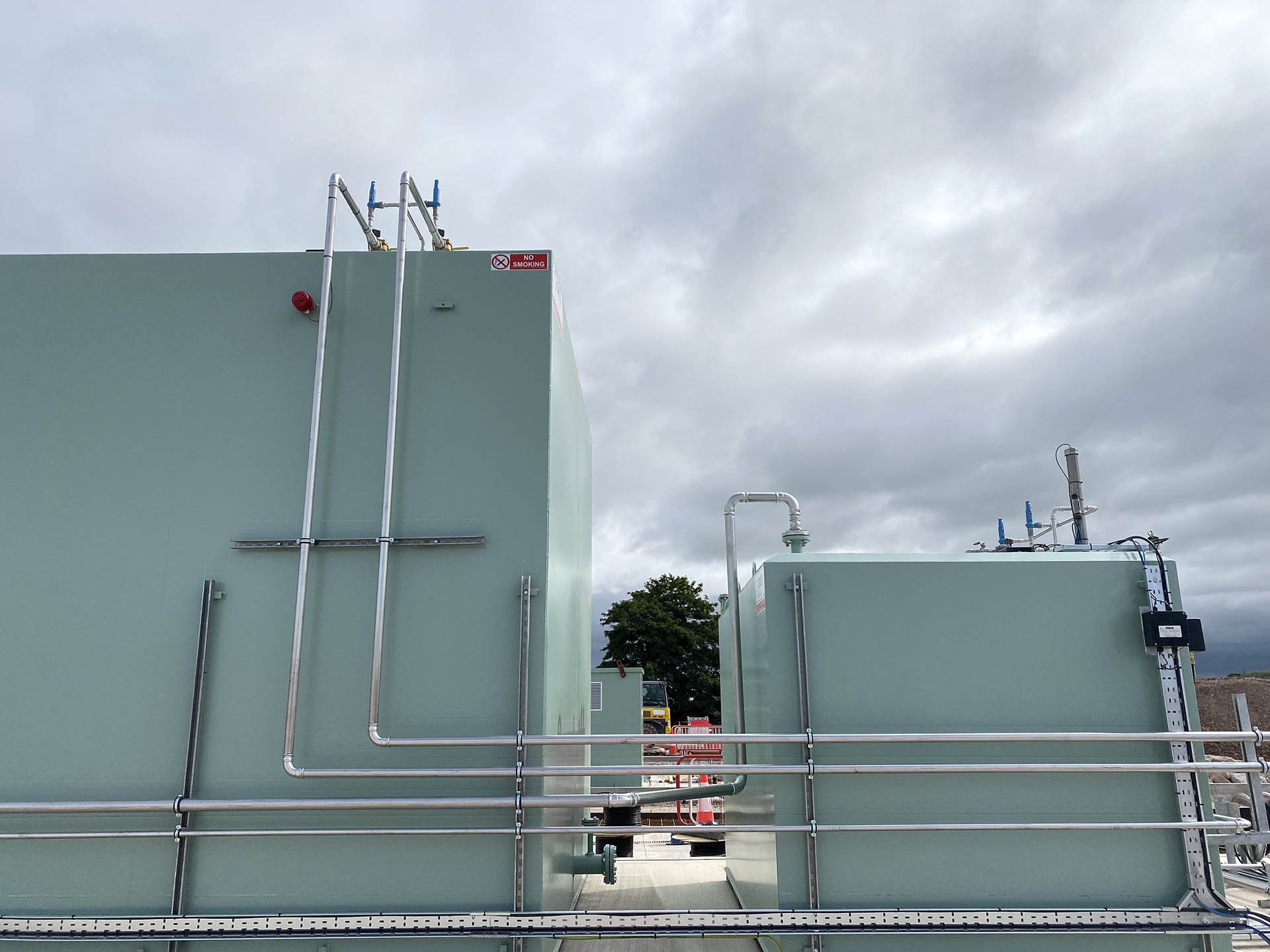